Warehouse Management System Migration
Project Summary
This project involved migrating a company’s outdated Warehouse Management System (WMS) to a modern, cloud-based solution. The transition aimed to streamline warehouse operations, improve scalability, and enhance automation across multiple distribution centers. By implementing the new system, the company optimized order processing within the Order Management System (OMS), gained real-time visibility into operations, and reduced overall operational costs, ensuring faster and more efficient service for customers. This migration was part of a broader strategy to modernize the company’s supply chain infrastructure and phase out legacy systems.
Problem Statement
The company’s existing WMS was built on aging technology that was expensive to maintain and lacked the flexibility needed for modern supply chain demands. This resulted in slow order processing, limited scalability, and difficulties in integrating with newer systems. As the business grew, these limitations caused inefficiencies, hindering the company’s ability to deliver timely and accurate services to customers. A new, scalable, and automated solution was required to support long-term growth and operational efficiency.
Key Objectives
• Cloud-Based WMS Implementation: Migrate from the legacy WMS to a cloud-based solution to enhance system flexibility and scalability.
• Automation of Key Processes: Increase automation in key warehouse processes, such as order tracking, to reduce manual efforts and improve accuracy.
• Real-Time Order Processing: Enable real-time visibility into order processing and fulfillment
• System Integration: Ensure smooth integration of the new WMS with the existing systems and third-party applications.
• Automation of Key Processes: Increase automation in key warehouse processes, such as order tracking, to reduce manual efforts and improve accuracy.
• Real-Time Order Processing: Enable real-time visibility into order processing and fulfillment
• System Integration: Ensure smooth integration of the new WMS with the existing systems and third-party applications.
Solutions Implemented
• A Cloud WMS will replace a costly legacy system, allowing for flexibility & automation
• Integration layers will connect the Cloud WMS to the OMS to enable real-time updates for order status, returns processing, and shipment tracking
• Integration layers will connect the Cloud WMS to the OMS to enable real-time updates for order status, returns processing, and shipment tracking
Outcomes Achieved
• 37.1% reduction in order processing time
• 60% reduction in manual returns processing
• 12.8% capacity increase per pilot site
• $750,000 saved over 3 years, driven by lower operational expenses
• 60% reduction in manual returns processing
• 12.8% capacity increase per pilot site
• $750,000 saved over 3 years, driven by lower operational expenses
Responsibilities
(See my Core Responsibilities across all projects)
• Collaborated closely with business stakeholders to document the current state process for warehouse and order management workflows, and partnered with development teams and the vendor to define and document the future state process, ensuring alignment with business goals and system capabilities.
Technologies Utilized
• Message Queues (MQs): Used for real-time communication between the WMS and OMS, handling sending shipment confirmation, order status updates, and returns processing
• Kafka: Utilized for real-time data streaming and event-driven architecture, enabling communication between micro-services for order processing, returns, and tracking.
• Micro-services: Deployed as independent, modular services for handling order processing, shipment tracking, and returns management
• Kafka: Utilized for real-time data streaming and event-driven architecture, enabling communication between micro-services for order processing, returns, and tracking.
• Micro-services: Deployed as independent, modular services for handling order processing, shipment tracking, and returns management
Current State Process Flow (before migration)
This process flow has been simplified and modified to protect confidential information.
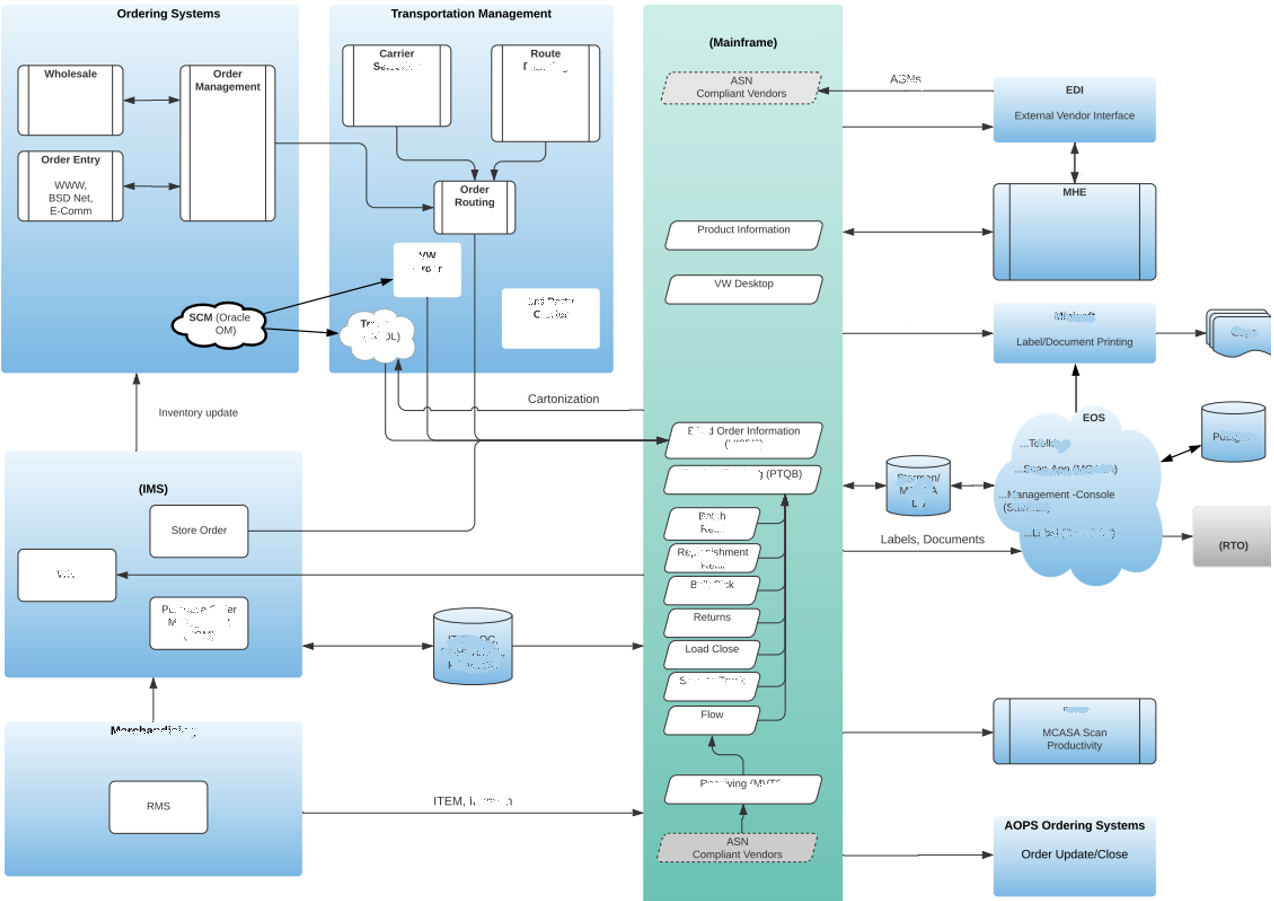
Future State Process Flow (after migration)
This process flow has been simplified and modified to protect confidential information.
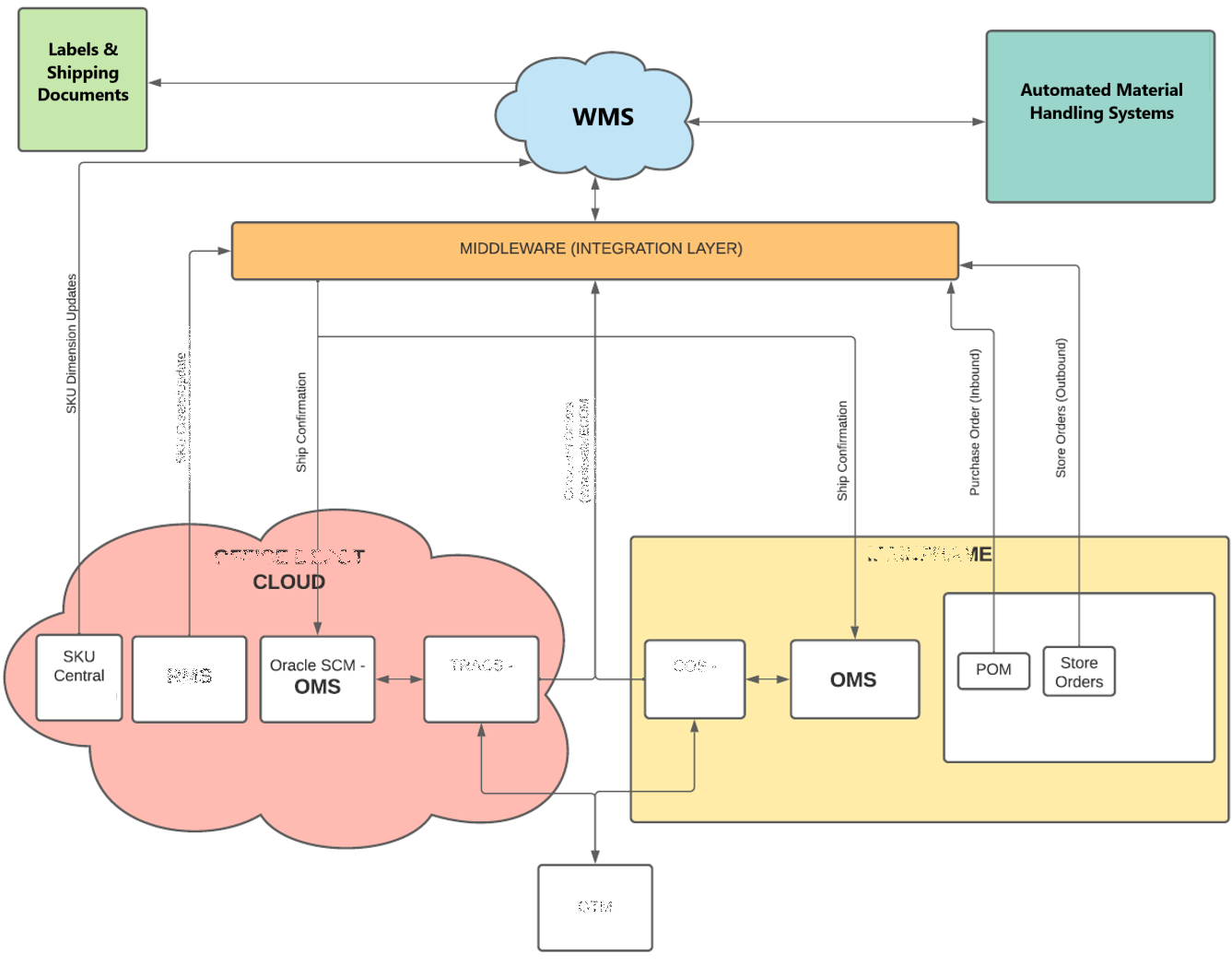